Modular Home FAQ
Some of the most commonly asked questions by home buyers; answered below!
Simply put, a modular home is a home built using modular construction. Modular construction occurs off-site and inside a facility rather than at the property where the home will be permanently located. Sections of the home, known as modules, are constructed inside the facility and then transported to the property and assembled. Once the modules are assembled, a modular home looks like any other house.
Modular homes are different from manufactured homes, sometimes called mobile homes. Manufactured homes are built on a permanent steel frame and moved using wheels and axles on that steel frame. Because the steel frame is integral to its construction, a manufactured home can be moved to another location. Unlike manufactured homes, a home built with modular construction is transported on a carrier. Once it is on the property, it is moved off of the carrier onto a foundation and assembled. The home becomes permanent to the property.
Modular homes can have attached, detached, or integrated garages. An attached or integrated garage share at least one wall with the modular home. These types of garages require some planning during the initial purchase, site check, and site prep of your home. They can be constructed later if necessary, but it will be a more complicated process than adding a detached garage. If you’re thinking of adding an attached garage to your modular home at a later date, consider ordering the siding and other exterior materials to match the home at the same time that you order your home. It is not uncommon for siding manufacturers to discontinue or change colors and you want to make sure you have enough of the right color to match your home.
Adding an attached garage as soon as the home is set is advantageous in that your siding, roofing, windows, and other exterior materials will match your home and you can include the garage as part of your construction loan and subsequent mortgage.
In choosing a garage for your home, work with your builder to determine the best type. If you’ve chosen a floor plan with an integrated garage, the choice of style and size are part of the floor plan. For floor plans where an attached garage is available, you can choose whether to have your builder install it at the same time your modular home is installed, or you can choose to build it at a later date. Most modular builders will be more than happy to accommodate a garage build at the same time as they construct your modular home. However, very few will come back to build your garage at a later date, so plan on finding a general contractor to build your garage if you choose to build it later.
A common question asked by people unfamiliar with homes built using modular construction involves how these custom homes are erected and affixed to the permanent foundation. The process of affixing each module to the permanent foundation and joining the modules together is known as a “set.”
A modular home is built on a reusable carrier. The home is delivered to the site with large trucks called toters. Before the home is delivered, the home’s foundation will already be complete. The home will either be set with a crane or rolled onto the foundation using a beam system. The builder will use the method most appropriate given the type of home, the site, and the type of foundation.
Typically, a modular home set will begin in the morning. The set crew will arrive, inspect the site, help place the crane on the site in the ideal location, and begin working to position the modules near the crane in the order they will be set. Because a modular home is built on jigs in a factory, it is perfectly square. Most foundations, on the other hand, are built on site and may not be perfectly square. This is a normal part of installation of a modular home. The set crew will adjust for these minor imperfections and determine the optimal placement of each module. Once the home is set, it will be secured to the foundation and the modules will be permanently joined together.
The first module usually takes the longest to set. Placement of each module depends on the placement of that first module, so set crews take great care to make sure the first module is precisely where it needs to be.
Homes built with modular construction are highly engineered and are required to meet both local and standard residential building codes. Most homes are set and completely weather tight in one day. Some more elaborate homes will require a second day or more for completion. Because of the efficiencies in modular construction, the process allows for a completed home under roof in just days.
The entire process of building a home using modular construction generally takes 6-9 months from purchase to occupancy. Depending on the complexity of the home, and any additions like porches or garages, a home built using modular construction can take an additional 6-12 weeks to be move-in ready once set.
Modular is a construction process, not a type of house. Modular construction uses the same grades of lumber and the same construction components as a local general contractor building a house the traditional way. Homes built using modular construction, therefore, can receive an addition any other traditionally-built home can have.
In fact, many modular home manufacturers offer modular additions that can be added to existing homes, either a home that has been built using modular construction, or a traditionally built house. With an addition using modular construction, the majority of the construction occurs off site and inside a facility. This means homeowners experience less disruption to their daily lives as the construction does not occur in their home. A modular home addition, once complete, appears as a fully integrated part of the home. The most popular type of addition is one that is attached to the side of a home to create additional living quarters, frequently called a mother-in-law suite. Additions can also include additional living space, kitchen, or extra bedrooms and bathrooms.
The quick answer is: absolutely! A common misconception about building a home with modular construction is that you cannot customize the floor plan to fit your needs. Modular doesn't mean picking a floor plan from a catalog. Because a modular home is simply a traditional home built inside a facility, you still have many customization options available to you.
Manufacturers using modular construction will offer a variety of starter floor plans. You can then create customizations that fit your needs within each floor plan. Many manufacturers will also allow you to build a completely customized floor plan.
Building a modular home can give you exactly the home you want. And the process of creating a custom floor plan can be easier than you might imagine.
The exterior walls of a home have several functions. Exterior walls play an important role in providing disaster resistance and energy efficiency. Exterior walls help minimize the air exchange between the outside and inside of your home. In addition, exterior walls provide a sound barrier against all kinds of outside noises.
But how thick are exterior walls? In many areas of the U.S., current IRC code calls for 2x6” framing with ½” sheathing on the exterior and ½” drywall on the interior. Modular homes meet standard building codes for your local area. Your modular home should have a standard exterior wall thickness of 6-1/2”, but always double check.
As a result of the code requirements, modular homes are just as strong as traditional homes. They can withstand high winds and earthquakes just as well, if not better, since they are also built to be transported.
Because of the unique building process of modular homes, many wonder if they can include a basement as the foundation of their modular home.
Like homes built the traditional way, a home built using modular construction is often placed on a full basement. The basement will be dug and constructed at your site using traditional methods. Once the basement is complete and the modules have been built off-site, your builder will arrange for transport of the modules to your site where they will be either rolled onto the basement using a roll system, or lifted into place with a crane
It's easy to confuse manufactured and modular homes!
A manufactured home has a clear definition created by the U.S. Department of Housing and Urban Development. According to the HUD.gov website, “A manufactured home (formerly known as a mobile home) is built to the Manufactured Home Construction and Safety Standards (HUD Code) and displays a red certification label on the exterior of each transportable section.” In their definition, HUD continues to explain that “the HUD Code, unlike conventional building codes, requires manufactured homes to be constructed on a permanent chassis.” A HUD home comes with a title and in many states requires the purchaser to pay sales tax on the purchase price of the home.
In contrast, a modular home is a home built in sections with all-wood construction and no permanent chassis. These homes are built in a temperature-controlled indoor facility using the same state, local or regional building codes as site-built homes.
A home built using modular construction is delivered to the site 80% complete. However, there is still about 20% of the finish work that needs to be completed once the home is set. This work includes finish work on the drywall, flooring, and ceiling areas where the modules come together, as well as setting doors or installing countertops that might start in one module but flow into another. On the exterior of the home, siding and shingles will need to be integrated between the modules. Also, the homes plumbing, electrical and HVAC systems will need to be completed on site and connected to the systems built in to the home
The builder selling the home usually completes the final finishing work. Some customers choose to complete some of the work themselves, either because they want finishes not offered by the builder, or they are hoping to save money by doing the work themselves.
When it comes to building any home, there are so many variables that play into pricing. Technically speaking the price per square foot of a home is simply the total cost of the home divided by the total square feet. When trying to compare prices of homes, be sure to compare apples to apples. In the home building industry, there is no official standard for what constitutes a square foot. One price might include the framing, drywall, electrical and plumbing, but none of the interior finishes like flooring, cabinetry, and finish bathrooms. A price from another builder might include all of that, plus high quality flooring, fixtures, cabinets, and foundation.
If you are trying to compare the cost of a modular home and the cost of a stick built home, be sure each builder has identified every cost associated with your build, including building blueprints and plans, building materials, inspections, labor costs, bids from subcontractors, foundation, and utilities just to name a few.
Also, be sure to understand what square footage number someone is using. Is it a livable square feet, or simply the square footage calculated using the exterior dimensions of the house? Livable square feet does not include porches, garages, and unfinished space like attics.
Not every square foot of a home is like every other. One square foot in a bedroom might include the joist, sub floor, carpet, drywall ceiling, and attic space. One square foot in the kitchen might include everything in the previous example plus upgraded countertops, tile backsplash, and elaborate hardwood custom cabinets.
Likewise, a price per square foot of a 1,500 square foot house built to the minimum code standards will be much lower than the price per square foot from a builder who includes higher quality building material and upgraded finishes standard in the price. You must also figure out if the foundation is included in that square footage price, and what type of foundation it is.
Asking the cost per square foot of a home is like asking a car salesperson what the cubic foot price is of their cars – it depends on the type you’re purchasing and the features it has!
Modular homes are built to the same building codes as a site-built home. The advantage is that portions of the home, called modules, are built inside a facility and protected from the elements during the building process. No wet lumber or construction delays due to inclement weather. But that is just one advantage to building modular. Because the modules are delivered to your site on carriers, they are built to withstand transportation over a variety of roadways. Adding to this the several stringent quality controls during construction, modular homes become much more durable and resilient than site-constructed houses.
And the advantages of building a modular home don’t stop at just the building process. When you visit a model center, not only can you look through many floorplans and customize those floorplans to fit your individual needs, you can also choose your décor and other options all at once, making the whole process easier for busy families. You may also modify your home (modular or site-built) in the future by adding new modules, easily expanding your house according to your needs.
Because the process is streamlined, modular homes typically cost less than a comparable site-built home and appraise at the same level as a site-built home. Despite this fact, they can still be financed through conventional means, making it possible to use the most profitable funding option available.
So generally, with modular homes, you get the same quality as a site-built home that’s built faster due to fewer delays, at less cost but with the same value. That’s a lot of advantages.
While modular and manufactured are often confused, modular homes are built to the same local and state building codes as a site-built home. They are transported to your site, removed from the carrier, and placed on a permanent foundation.
Manufactured homes, often referred to as mobile homes or trailers, are built on a permanent steel frame and moved using wheels and axles on that steel frame. Because the steel frame is integral to its construction, a manufactured home can be moved to another location.
Modular homes, like a site-built home, are permanent to the property and appraised as such.
The short answer is, yes. Modular home floor plans are just a starting point to your dream home. Homeowners often make changes to floorplans ranging from stretching the plan to make rooms bigger to changing the location of rooms completely. Sometimes a homeowner may combine rooms to make one big room or flip a floorplan so that the utility room is on the opposite side of the plan. Homeowners have taken aspects they liked from two different floorplans and combined them, or have even submitted their own plans for a completely customized home.
While modular homes are customizable, just like site-built homes, they are subject to certain regulations and any customization will need to meet those requirements. In addition, each manufacturer has restrictions on different aspects of customization that your builder can discuss with you.
Modular homes can have any aspect that a site-built home has, including an attic. The roof pitch you choose will play a role in whether your home can ultimately have an attic, as well as the manufacturer you choose. Each manufacturer will have a variety of both interior and exterior options, like attic storage space or stairs. So if an attic is important to you, your builder can help you identify the best manufacturer and floor plan for you.
Unlike manufactured homes, often referred to as mobile homes or trailers, modular homes do not have titles. Where manufactured homes are built on a permanent steel frame with wheels and axles, which allow them to be moved to different locations, modular homes are transported to the property on temporary carriers and placed on a foundation.
Like a site-built home, modular homes are appraised as a permanent fixture on the property, so do not require a title. Modular homes are also built to the same local and state building codes as a site-built home.
Homes built using modular construction are becoming a popular choice for many people and families. Choosing modular construction can be a relatively quick and frequently less expensive option. The affordability and faster build time may leave many homeowners wondering if modular homes are durable enough to hold up in hurricanes and tornadoes.
Modular homes have several advantages over traditional, site-built homes. While both construction methods must adhere to the same building codes and meet the same wind, snow, and seismic standards, modular homes have stringent inspections at each stage of construction, ensuring every home is well-built and meets all necessary codes. Conversely, a traditionally-built home receives much fewer inspections, and sometimes just one at the end of construction.
Modular homes have between 15% - 20% more wood per square foot which increases their sturdiness and ability to stand up to severe weather. In addition, to enhance the stability of each module, many modular home manufacturers both glue and screw the drywall into place.
Research shows homes built with modular construction fare even better than a traditionally built home under extreme weather conditions like hurricanes and tornadoes. modular homes outperform traditional homes in extreme weather condition. After Hurricane Andrew in 1992, FEMA commissioned a study comparing site-built homes to both manufactured and modular homes. In their report, called “Building Performance: Hurricane Andrew in Florida,” FEMA concluded that modular homes withstood the storm “far better” than site-built housing. “Overall,” the report stated, “relatively minimal structural damage was noted in wood-framed modular housing developments. The module-to-module combination of the units appears to have provided an inherently rigid system that performed much better than conventional residential framing. This was evident in both the transverse and longitudinal directions of the modular buildings,” according to the report.” (Publication number FIA-22, item 3-0180)
Unlike manufactured homes (often called mobile homes), a modular home cannot be moved. Once it is transported and removed from the carrier, it becomes permanent for the property, just like a standard site-built home.
Modular homes do not differ much from site-constructed homes when placed on a property, as they also become permanently bound to it. This means that they can last as long as a standard site-built home, though often they are even more durable. This is because they undergo stricter quality control over different stages of construction.
Modular homes are also better suited to withstand natural disasters, including hurricanes, tornadoes, storms, or earthquakes. They are made from more materials and are stronger due to the aforementioned frequent quality controls. It’s impossible to say how long a modular home will last, after all, an average house can endure for from 50 to 100 years, but what we can say for sure is that they won’t last shorter than the site-built houses in the same regions.
Mortgage loans are secured by either land or real estate. Since modular homes are placed on a permanent foundation, they can be treated as a latter. This means that once such a home is installed, you can finance it through conventional methods, like a mortgage.
FAQ By Anthony Zarrilli, President of Zarrilli Homes
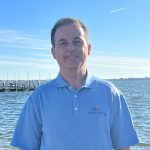
Modular homes are built in a factory somewhat like a car is built in a factory. Both can be built outside but which one do you think is built more efficiently both with time and money. For example, get all the parts of a car and put it in a parking lot and have assemblers there to put it together. Yes they will accomplish this and the car will run but now have it built in a climate-controlled facility with a person or persons that are skilled in each part of the assembly process build your car and see how well and quickly the build occurs. This is exactly the process with a modular home.
If the build is done properly there is a time and cost savings in building modularly. It really depends on the “builder” you choose to design and complete the home. I would suggest to them to do their research on the modular manufacturer and the builder and their reputations speak for themselves. The “cheapest” is never the best…
The beginning phase is designing the home, selecting the finishes, working on the financing, preparing the home site and submitting for permits, etc. All of which we at Zarrilli Homes, LLC holds your hand and walks you through. Once the physical work takes place all the questions are answered (all upfront work with customers as opposed to stick build that a lot takes place along the way). We the builder take it from the home foundation and modular set through completion. Typically I let customer know the upfront timeframe can go as quick as they like or as slowly depending on their decision-making capabilities. But normally from the time of first meeting to time, they would move in including but not limited to:
Home design, old home demo on property, selections, contracts/PO/agreement, financing, and then the home build, delivery, set and completion is 6-10 months. The variable timeframe again depends on the customers capability to make decisions and also the size and/or complexity of home.
No, it will not and I show them homes I have done from 500sq. ft to over 12,000sq. ft. I have built homes on the ocean in very high-end communities, a home next to John Stewart on the Navensink, and then 2000 sq. ft on a lagoon in Toms River. They sell at or above a stick-built home in their respective areas. I also hand them a list of the last few hundreds homes I built to drive by, walk through or contact owner for references as well.
No you do not and I tell them they can give me a plan out of a magazine, off the internet, from a competitor (stick or modular), hand drawn on paper need not be to scale, and I will draw it up on my CAD program Chief Architect. Then we can get a virtual plan inside and out and tweak the draft plans to their liking. I then put a price on it that typically is 95%+ on for them to make the decision to proceed. There really are no limits to what you can build modular with Zarrilli Homes, LLC. We are a fully custom modular home builder and to date building well over 1000 homes have not been able to build a modular that was asked of us.
The exterior walls of a home have several functions. Exterior walls play an important role in providing disaster resistance and energy efficiency. Exterior walls help minimize the air exchange between the outside and inside of your home. In addition, exterior walls provide a sound barrier against all kinds of outside noises.
But how thick are exterior walls? In many areas of the U.S., current IRC code calls for 2x6” framing with ½” sheathing on the exterior and ½” drywall on the interior. Modular homes meet standard building codes for your local area. Your modular home should have a standard exterior wall thickness of 6-1/2”, but always double check.
As a result of the code requirements, modular homes are just as strong as traditional homes. They can withstand high winds and earthquakes just as well, if not better, since they are also built to be transported.